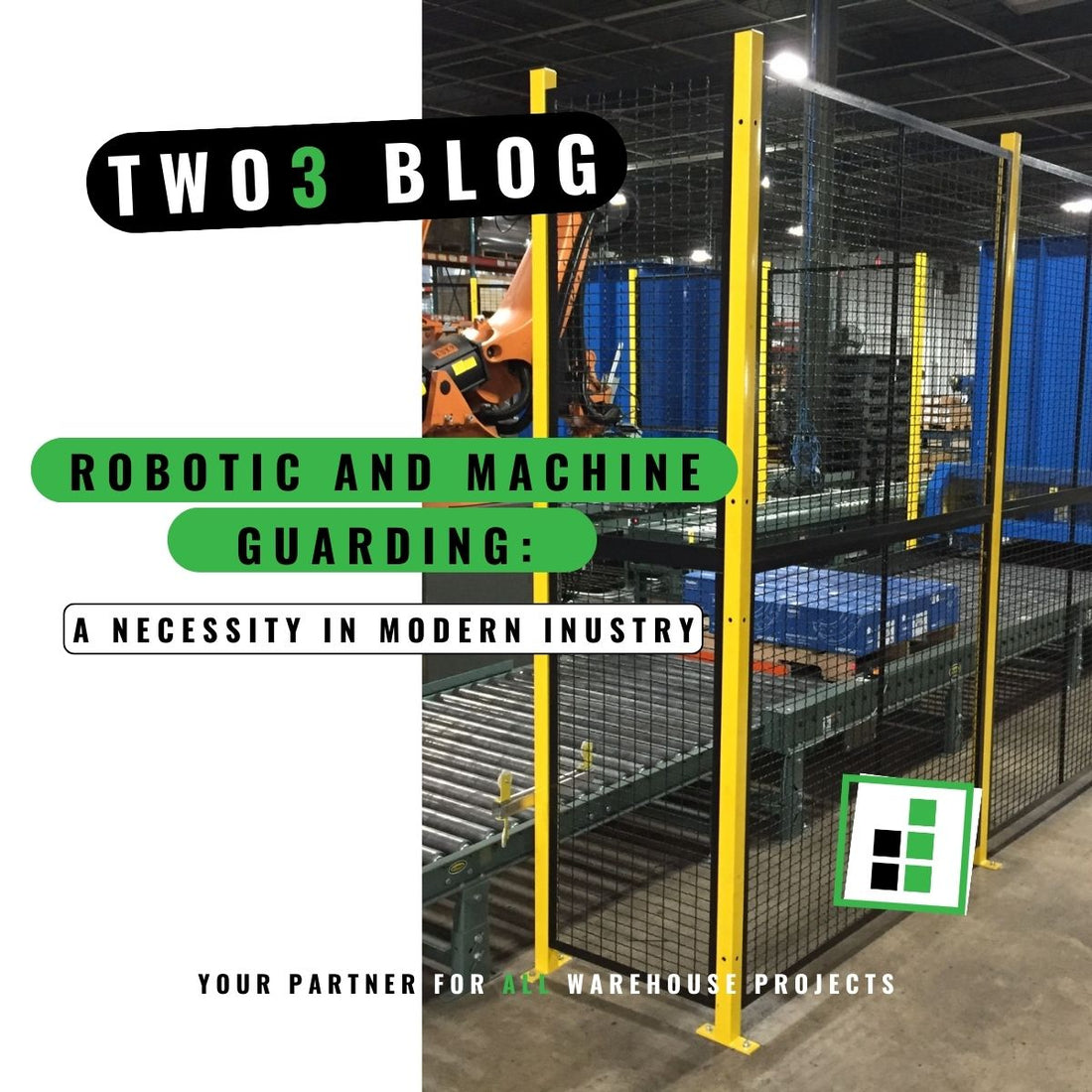
Robotic and Machine Guarding: A Necessity in Modern Industry
Share
Welding Robots, press brakes, and plasma cutters have become integral components of manufacturing processes. As the use for automating production equipment increases, so does the importance of safety measures for your visitors, employees and machine operators. Let's explore the significance of these guarding systems, the repercussions of neglecting them, and how they can be tailored to various business needs.
What is Wire Machine Guarding?
Machine guarding refers to the safety barriers, devices, and protocols implemented to protect personnel from the dangers of automated equipment. These systems provide a strong and economical solution to plant safety needs - designed to prevent accidental contact with moving parts, restrict access to danger zones, and contain debris from malfunctioning equipment.
When Should Guarding be Used?
- Moving Parts: Any machine with moving parts, such as gears, belts, or rotating devices, should have protective guarding. This prevents workers from getting caught, pinched, or entangled.
- Hot Surfaces and High Voltage: Machines that operate at high temperatures or use significant electrical power should be guarded to prevent burns or electrocution.
- Chemical Processes: Machines involved in chemical processing should have guards to prevent spills, splashes, or the release of toxic fumes.
- Robotic Arms and Automated Systems: Modern manufacturing units often deploy robotic arms that move with precision and speed. These should be guarded to ensure workers aren't accidentally struck or trapped.
Review OSHA 1910.212 and ANSI/RIA = R15.06-2012 - codes for more details.
Financial and Health Consequences of Neglect:
- Workplace Injuries: Without proper guarding, the risk of workplace injuries skyrockets. This can lead to prolonged hospital stays, rehabilitation, and even permanent disability.
- Financial Liability: Injuries result in compensation claims, increased insurance premiums, and potential legal action. The direct and indirect costs can be crippling for businesses.
- Operational Downtime: An accident can halt production, leading to missed deadlines, contractual penalties, and loss of business reputation.
- Regulatory Fines: Many countries have stringent occupational safety regulations. Non-compliance due to lack of proper guarding can result in hefty fines and legal ramifications.
Tailored to your business needs:
- Modular Guarding Systems: These are customizable guarding solutions that can be adjusted based on the layout and requirements of a factory. They offer flexibility as machinery is upgraded or reconfigured.
- Electronic Sensors: Advanced guarding systems come equipped with sensors that can halt machine operation if an unauthorized entry is detected.
- Interlocking Devices: These ensure that machines can't operate unless safety barriers are securely in place. They're particularly useful for machines that require frequent human intervention.
- Adjustable and Retractable Guards: For businesses that have multipurpose machinery, adjustable guards can be repositioned based on the operation being performed.
- Transparent Guarding: Made of durable materials like polycarbonate, these guards provide safety without obstructing the view, allowing operators to monitor the machine's performance.
Conclusion:
As industries evolve and machines become more intricate and powerful, the guarding systems protecting human workers need to be equally advanced. Investing in top-notch guarding solutions is not just about compliance; it's about valuing human life and the long-term sustainability of the business.